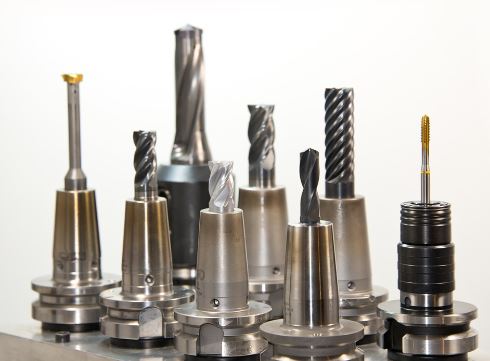
When investing in CNC machine tools, one must exercise the utmost caution and care. These precision instruments are the beating hearts of your manufacturing operations, and selecting a tool ill-suited to your needs could prove disastrous to production, quality, and profits alike.
The wrong CNC machine could grind your assembly line to a halt with incompatibility or downtime, produce parts riddled with defects that must be scrapped, or operate at a snail’s pace that hemorrhages money with every tardy component. Before taking the plunge, understand your workload requirements, then evaluate options for accuracy, speed, material handling, and other factors critical to your parts and process.
- Understand Your Needs
Before you start shopping for a CNC machine tool, it’s important to have an idea of what the machine will be used for. You’ll need to consider the type and number of parts you need to produce, as well as any specific requirements in terms of cutting speed and accuracy.
There are different types of CNC machines, such as milling and lathe machines, so it’s essential to understand the type of machine you need for your specific application. A glass drilling machine may be the best choice for drilling precision holes in glass, but it won’t be suitable for other types of materials. The types of materials you need to work with should also inform your decision.
- Consider the Machine’s Capabilities
Every CNC machine tool has its own set of capabilities and limitations. It’s important to consider these features carefully before making a purchase. Factors such as the size and shape of the parts it can handle, the maximum spindle speed, cutting force and accuracy should all be taken into account.
CNC machine tools networking capabilities are also essential. Many machines offer high-speed connectivity to software programs, allowing you to customize and control the machine remotely via computer or smartphone. This can be especially useful in complex production runs where multiple machines need to be connected together or monitored from a central location.
- Factor in Cost and Maintenance Requirements
The cost of a CNC machine tool will vary significantly based on the model, capabilities and features. It’s important to factor in both the initial cost of the machine as well as any ongoing maintenance costs. Some machines may require more frequent servicing and repairs than others, so it pays to research the expected long-term costs before making a decision.
CNC machine maintenance is also an important consideration. Machines that require frequent maintenance or replacement of parts can be costly to operate in the long run. Researching the expected lifetime and availability of spare components should help you make a more informed decision.
- Check Availability of Replacement Parts
Parts break down over time, so it’s essential to consider how easily replacement parts can be obtained. Reputable manufacturers typically offer a wide range of spare components for their machines, ensuring that you won’t have to wait long for repairs or replacements. It pays to research the availability of different makes and models before making a purchase.
If you’re planning to buy a used CNC machine, it’s also important to check the condition of any replacement parts that may be needed. Buying a machine with worn-out components can quickly become an expensive mistake.
When choosing a CNC machine tool, caution is key. While it may be tempting to hastily purchase the shiniest, most high-tech equipment on the market, doing so without careful consideration could prove a costly mistake. Different tools are designed for specific applications, so you’ll want to evaluate factors like required precision, material types, and production volume to determine what’s right for your needs.
You’ll also want to weigh the upfront costs of the machine against maintenance, repair, and energy requirements to ensure the lifetime value makes sense for your budget and workload. Like any major purchase, it pays to do your homework to find a CNC partner that’s a perfect fit, rather than one that leaves your resources and parts in the scrap heap.